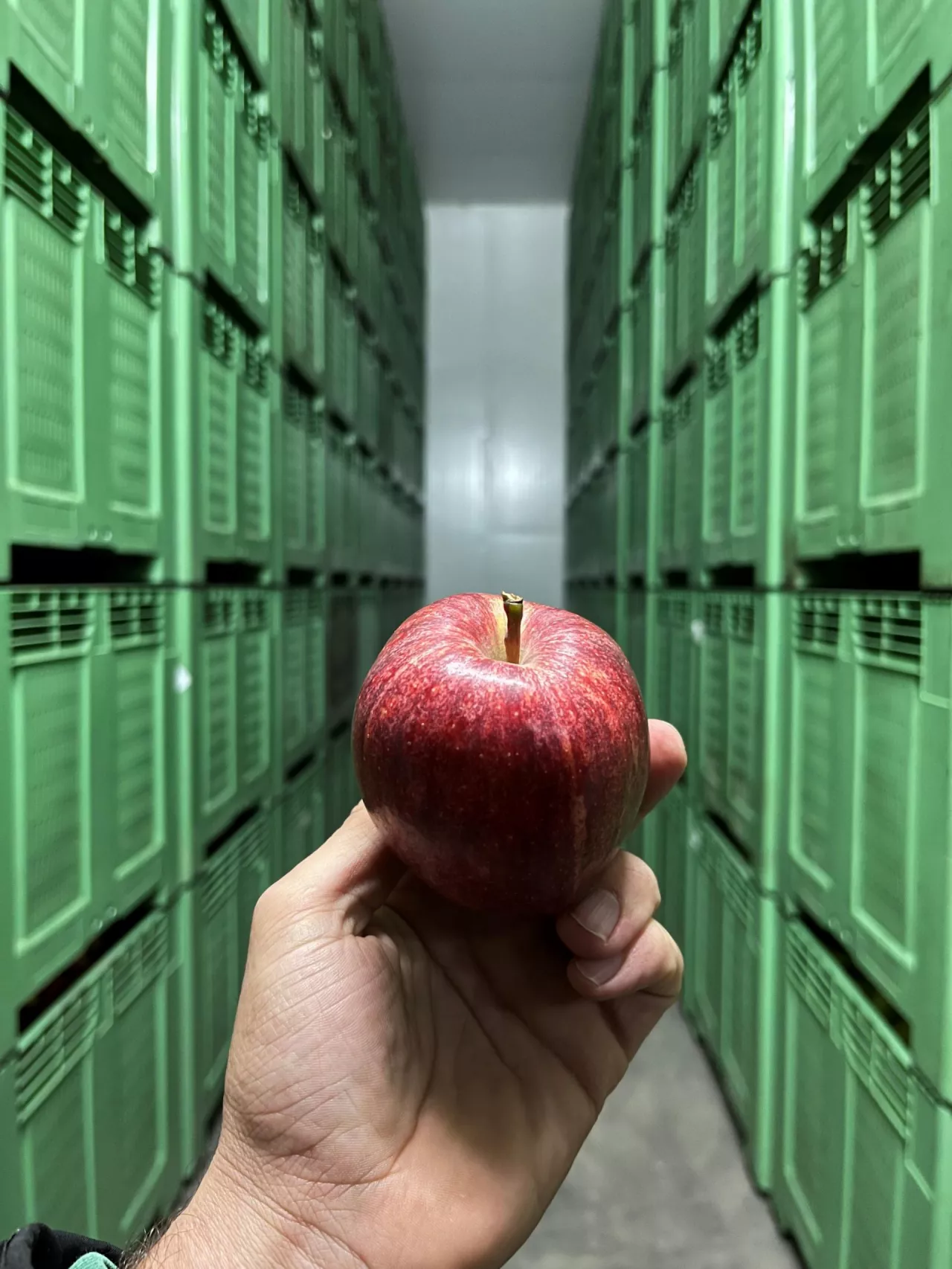
Odpowiednie przygotowanie obiektu przechowalniczego jest warunkiem niezbędnym do utrzymania wysokiej jakości pozbiorczej owoców. W wyniku zaniedbań w tym zakresie istnieje realne zagrożenie nieuzyskania optymalnych parametrów podczas przechowywania, takich jak temperatura, skład gazowy (CO2 : O2 ) czy wilgotność powietrza.
Może to skutkować znacznym pogorszeniem parametrów jakościowych przechowywanych owoców, a w skrajnych przypadkach – skróceniem okresu ich przechowywania oraz co najgorsze – uszkodzeniami spowodowanymi zbyt wysokim stężeniem dwutlenku węgla, zbyt niskim stężeniem tlenu, więdnięciem owoców czy zbyt niską temperaturą. Dlatego w odniesieniu do każdej komory, każdego obiektu przechowalniczego ważne są przegląd i konserwacja zamontowanych tam urządzeń chłodniczych oraz pomiarowych.
Po pierwsze: dezynfekcja
Po każdym sezonie przechowalniczym, niezależnie od tego jak długo przetrzymywaliśmy owoce, należy umyć ściany, sufit, drzwi, posadzkę, aby zlikwidować ogniska chorób grzybowych w komorach. W tym celu można zastosować detergenty wykorzystywane do mycia powierzchni w przemyśle spożywczym. Ściany zbudowane z paneli z rdzeniem poliuretanowym lub styropianowym oraz pokryte blachą można myć myjką wysokociśnieniową. Z drugiej strony ściany komór pokryte pianką poliuretanową należy czyścić delikatnie, ostrożnie, tak aby nie uszkodzić powłoki zapewniającej gazoszczelność. Dezynfekując komorę chłodniczą przed nowym sezonem przechowalniczym, ograniczamy źródło chorób grzybowych. Choroby te występują co roku, dlatego ważne są wszelkie działania zmniejszające źródło porażenia.
Sprawność urządzeń chłodniczych
Kolejnym krokiem jest sprawdzenie sprawności urządzeń chłodniczych. Najpierw należy ocenić wizualnie, czy chłodnica nie została uszkodzona podczas rozładunku komory oraz czy poprawnie pracują wszystkie jej wentylatory. W przypadku sprężarki należy sprawdzić poziom oleju oraz freonu. Olej w sprężarce na ogół jest wymieniany na nowy co dwa sezony pracy, choć w przypadku bardzo długo trwających okresów przechowalniczych wymiana bywa przeprowadzana również co roku. W przypadku freonu, jeżeli stwierdzimy jego ubytek, powinniśmy spuścić pozostały freon i sprawdzić szczelność instalacji. Następnie, po zlokalizowaniu nieszczelności, należy je zaspawać. Dopiero po upewnieniu się, że instalacja jest z powrotem szczelna, można ponownie uzupełnić gaz do optymalnego poziomu, co z pewnością przełoży się na wysoką wydajność układu chłodzenia. Nigdy nie należy godzić się na uzupełnienie poziomu czynnika chłodniczego bez uprzednio zlokalizowanych i naprawionych nieszczelności! W dalszej kolejności warto sprawdzać pracę skraplacza. Na ogół jest on umiejscowiony na zewnątrz budynku i nie jest osłonięty dachem, co umożliwia sprawne oddawanie ciepła do otoczenia. Często więc jest tak, że wentylatory skraplacza zasysają liście, kurz itp., co ogranicza możliwości wymiany ciepła z otoczeniem, w efekcie czego sprawność skraplacza jest obniżona. Dlatego po każdym sezonie należy wyczyścić go sprężonym powietrzem, wydmuchując zanieczyszczenia znajdujące się pomiędzy lamelami.
Urządzenia modyfikujące atmosferę
Drzwi komory chłodniczej
Nie wolno pominąć oceny stanu technicznego drzwi chłodniczych, ramy, ościeżnicy. Należy starannie ocenić stan uszczelek gumowych, a także przylgnie na powierzchni ościeżnic oraz na progu, który wraz z uszczelką progową jest punktem, w którym często dochodzi do uszkodzeń. Nie wolno pominąć mimośrodowych mechanizmów docisku drzwi do ościeżnicy. Poza tym bez oceny nie pozostawiamy okienka inspekcyjnego.
Kontroli podlegają:
- uszczelka;
- przylgnie;
- zawiasy oraz zamek okienka.
- Należy sprawdzić również stan zaworów kulowych, jako że w dużych obiektach często są uszkadzane przez wózki widłowe.

Urządzenia pomiarowe
Ważną czynnością, o której nie wolno zapominać i należy przeprowadzać rokrocznie, jest sprawdzenie podłóg gazów wzorcowych lub kalibracja urządzeń pomiarowych do mierzenia stężenia CO2 i O2 w komorach chłodniczych, zwłaszcza w obiektach, w których przechowuje się jabłka w atmosferach zawierających <1,2% tlenu. Urządzenia zamontowane zarówno w płuczkach, jak i w ręcznych analizatorach powinny zostać skalibrowane gazami wzorcowymi. Ocenie poddajemy również poprawność działania termometru. Odczyt z wyświetlacza można porównać z termometrem rtęciowym, który należałoby zamontować przy czujce temperatury w komorze chłodniczej. Prostym sposobem jest włożenie czujnika temperatury do topniejącego lodu, używając w tym celu wody destylowanej. Termometr powinien wskazać 0°C.
Testy gazoszczelności komory
Spełnianie wysokich wymagań konsumenta wymusza na sadownikach przechowywanie jabłek przy bardzo niskich stężeniach tlenu w okolicy 1%, co można uzyskać tylko w bardzo szczelnych komorach. Najczęściej nieszczelności występują przy zużytej uszczelce okienka inspekcyjnego czy też drzwi gazoszczelnych, a ponadto przy połączeniach pomiędzy panelami, w narożnikach pomiędzy ścianami a sufitem i posadzką. Miejscem nieszczelności bywa również sama posadzka. Po kilku latach obciążenia posadzka delikatnie opada i powstają nieszczelności pomiędzy ścianami komory a posadzką. Nieszczelności należy również szukać przy łączeniach płyt. Testy szczelności przeprowadza się w obiektach z KA, przy zamkniętej komorze z włączonym zaworem bezpieczeństwa. Za pomocą odkurzacza starego typu należy wytworzyć nadciśnienie rzędu 20 mm słupa wody. Ustalamy takie ciśnienie, wykonując z przezroczystego przewodu tzw. U-rurkę. Jeden z jej końców przymocowujemy do króćca zamontowanego w drzwiach chłodniczych, a drugi przyklejamy do drzwi i zalewamy wodą. Wzdłuż U-rurki montujemy podziałkę milimetrową, dzięki której wyznaczymy moment uzyskania oczekiwanego, wspomnianego wyżej nadciśnienia. Jeśli spadek ciśnienia z 20 mm do 10 mm będzie trwał ponad 30 minut, to taki czas jest akceptowalny dla komór typu ULO. Jeżeli ten czas wyniesie do 20 minut, to szczelność takiej komory jest wystarczająca dla warunków KA. Należy zachować szczególną ostrożność przy sprawdzaniu gazoszczelności komór, gdyż wytworzenie większego nadciśnienia niż 20 mm słupa wody, może doprowadzić do rozszczelnienia komory, a w skrajnych przypadkach przy wytwarzaniu podciśnienia – do oderwania od ścian paneli z rdzeniem poliuteranowym/styropianowym.
Marek Grzęda AgroFresh Polska